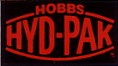 
Hobbs Pak
HOBBS REAR LOADER
    Although they never built a front loader, Hobbs jumped in to the rear-loader race in 1967 with a hinged-hopper packer very similar in function to the Heil Colectomatic, though there were some important and interesting differences. The new Hobbs Rear Loader (HRL) used a toggle linkage to actuate the packing panel, which resulted in faster operation, plus torque multiplication near the end of the blade travel path. Hobbs also used inexpensive and easy-to-service single stage, single-acting cylinders (outside the tailgate) to lift the hinged hopper section. The hopper dropped back down into place by gravity. By comparison, the Heil system used double-acting telescopic cylinders mounted beneath the hopper.
The groundbreaking 1967 Hobbs Rear Loader, with body corners radiused 9"
    Perhaps most striking about this rear loader was the construction of the body, which resembles a squared-off tube, with continuously welded braces girdling the diameter of the structure. This type of body design would become popular among the west coast front loader manufacturers, with slightly more curvature for improved strength-to-weight ratios. Despite this seemingly advanced body construction method, Hyd-Pak (for reasons unknown) replaced it shortly after introduction with a more conventional rectangular braced version. One possibility for the change may have been that it was unnecessarily expensive to build such a strong body, in an era when most rear loaders only packed around 500-600 pounds per cubic yard. All Hyd-Pak rear loaders were full eject type, with dual side electric packing controls.
INSIDE THE HOBBS REAR LOADER (HRL)
|
    The Hobbs Rear Loader (HRL) employs the same theory of operation as the Heil Colectomatic, whereby the the hopper consists of a separate hinged assembly which is pivotally connected to the lower rear edge of the tailgate. The hopper is raised during the pack cycle, and swept clean by a pivoting packer panel, which compresses the refuse in the body.
    What sets the HRL packer apart from the Colectomatic is the toggle linkage used to operate the packer panel. This arrangement multiplies the force of the operating cylinders, resulting in lower system pressure. Also, the hopper is raised and lowered by two side-mounted cylinders affixed to the tailgate sidewalls.
|
    This is the 'home' position, with the generous 1.75 cubic-yard hopper lowered to receive refuse. The packer plate is fully closed, and retaining any previously packed refuse within the body.
|
    Using either of the right or left side push-button electric controls, the operator begins the cycle, with the packer plate opening high over the hopper. There is ample room to 'heap' refuse without the worry of it being pushed out the hopper by the packer plate.
|
    Next, the hinged hopper beings its ascent, being lifted by the side-mounted cylinders, riding behind T-shaped flanges to protect against pinched fingers. The cylinders can't be contaminated by refuse or liquids which may seep underneath the hopper.
|
    Once fully raised, the hopper completely seals off the mechanism, preventing injuries and the possibility of spraying liquids on the operator. Through the toggle links, the packer cylinders apply 83,000 pounds of force against the refuse. Once the hopper is cleared, the bucket is lowered by gravity, its own weight pulling it back down to the loading position. Elapsed cycle time: 17 seconds.
|
Tailgate raised on a 20-yard model HRL
The HRL featured a high-mount horizontal ejection cylinder, which projected into the blade
Just a year after its debut, the HRL model got a conventional box-brace body
Hand-loading a 20-yard HRL on a Ford F-Series Super Duty conventional
    By the early 1970s, the Hyd-Pak was re-branded as the Hobbs-Pak line of refuse equipment. The old 60-Series side loaders carried on, now called the TDSL (tilt-dump side loader) and available up to 24-cubic yards. These models were soon being mated with the advanced new Automated Side Loader (ASL) arms being developed independently by several western manufacturers. These lightweight Hobbs packers were ideal platforms for ASL systems. The full-pack M-Series side loaders were similarly re-named the POSL (push-out side loader).
    Hobbs also produced a range of transfer trailers and transfer station equipment, route trailers and stationary packers. The HRL rear loader received some minor body changes, and was available in sizes up to 25-cubic yards with container attachments. In 1973, the rear loader was revised again, becoming the HRL-300 series. The toggle-link packer linkage was eliminated, in favor of a more conventional layout identical to that of the Heil Colectomatic Mark III. By the end of the 1970s, Hobbs appears to have exited the refuse body market altogether, though the company continued to build trailers as a division of Fruehauf for several years.
Hobbs-Pak TDSL circa 1972
Early 1970s Hobbs-Pak HRL with a 25-yard body and container loader
1972: Top-loading packer trailers (up to 80 cubic yards) handled the long hauls
Revised completely in 1973, the HRL300-Series rear loader was little more than a clone of the Heil Colectomatic Mark III.
This 1977 model is one of the last of the breed.
Hobbs-Pak TDSL with Litter Lift ASL attachment, Phoenix Arizona, 1978
SELECTED PATENTS
Patent # |
Description |
Inventor |
Assignee |
Date |
US3456821 |
Refuse Loader with Toggle Action |
Pappas, et.al. |
Fruehauf Corp. |
August 14, 1967 |
US3452891 |
Refuse body with side loader |
Wilson, et.al. |
Fruehauf Corp. |
March 5, 1968 |
3/5/06 (revised 7/4/22)
© 2006, 2021, 2022
All Rights Reserved
Logos shown are the trademarks of respective manufacturers
Photos from factory brochures/trade advertisements except as noted
|
|
|
| |