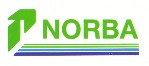
Norba Linea RL25 / RL30 Rear Loader
   
During the late 80s or early 90s, Norba once again introduced new rear loader models on the market. Designated RL25 and RL30, they were not simply variations of previous models, but entirely new designs! The new models were essentially slide/sweep packers, but with some quite unique twists. These still featured two panels acting together and carried by slides in the tailgate sidewalls, but that is where the similarities ended.
    Unlike on normal slide-sweep designs, where the lower slide blocks/rollers are typically connected to the lower end of the slide plate (where the slide and packer plates are hinged together), the lower blocks (15) on the RL25/RL30 were connected by the same pin (26) that connected the packer piston ends to the packer plate fulcrums (16). These pins simply extended out on the sides, protruding through the centers of the slide blocks. Because of this, the slide and packer plate hinge was free to move backwards and forwards as the packer plate opened and closed, unaffected by the side wall tracks.
The upper portion of the slide plate was connected to the upper slide blocks (14) by the same pins (22) that held the upper ends of the packer cylinders in place.
Slightly below and forward of the upper slide blocks there were removable pins (25) extending from the slide plate, and out through slots in the sidewalls, just below the upper portions of the slide tracks. These pins were connected to the piston ends of the slide plate cylinders, which were placed outside the tailgate, and hidden behind covers. This gave the slide cylinders a positive thrust during the final stage of the pack cycle, enabling maximum force as the load was compacted into the body.
   This design gave the RL25/RL30 a unique behavior compared to normal slide-sweep rear loaders. As the packer plate opened, advancing backwards over the load in the hopper, the lower end of the slide plate also swung backwards. As the packer plate closed, the lower end of the slide plate swung forwards, pushing the load against the front face of the hopper. This created a "pre-compaction effect" within the hopper. As a result of this, the slide plate was not parallel to the slide tracks, when the packer plate was in its inner position. Thus, the use of a "fixed" divider wall (as used in all other slide-sweep packers except the Heil Mark IV and Mark V) was not possible. Instead, the divider wall (29) was not fixed, but consisted of a large flexible steel sheet with a stiffener plate welded to the lower end. It swung forwards and backwards as the packer assembly moved, basically acting like a giant leaf spring. Another result was that the hopper bottom (39) wasn't circular like on most rear loaders, but elliptical, sloping forwards. This made the hopper unusually deep relative to the tailgate length.
INSIDE THE NORBA RL25 / RL30
|
1. The packer is in its home position, and the packer sequence is ready to be initiated
2. The packer cylinders retract
|
3. The packer plate is now fully opened, and the slide plate is parallel to the slide tracks
4. The packer assembly is pulled downwards by the slide cylinders
|
5. The packer assembly has reached the lower position
6. The packer cylinders extend, swinging the packer plate inward. The slide plate also swings inward
|
7. The packer cylinders are fully extended. Note the distance between the packer cylinders and the packer-slide plate hinge: the large distance provides unusually high torque to the packer plate
8. The packer assembly is pushed upward by the slide cylinders, compacting the load into the body
|
    Two versions were offered, the heavy-duty Linea RL30 and the lighter duty Linea RL25. The RL30 was a full-width body, intended to handle both residential and commercial routes. It could be equipped with both bin lifters and container slots. The RL25 was probably intended for residential collection only, and the tailgate was both narrower and shorter than on the larger version. The packer was also lighter and the swept volume reduced. The RL25 had a smaller overall body height. The two versions are easily distinguishable as the top plane of the RL30 tailgate slopes backwards, whereas on the RL25 it is horizontal.
    The rear part of the body was also different compared to normal rear loaders. Instead of flat, sloping rear side faces, the upper quarters had an additional slope. This was done to conceal the tailgate lift cylinders, which were hidden inside the angled side beams. Like on most Norba refuse bodies, the cylinders initially pushed the tailgate vertically, releasing it from the locking latches at the bottom sides of the body, and then swung it backwards and upwards.
    Unfortunatly,the RL25/RL30 were short-lived designs, and production might even have been stopped within half a decade. The reasons for this are unknown, but it is very probable that the complexity of the design became its downfall. The flexible divider wall might have caused problems, and maybe the packer plate fulcrums broke due to the asymmetric load. Or, perhaps it might not have provided compaction ratios that were significantly higher than those the more conventional Ki-11/RL35 series.
The Norba RL25/RL30 used an oscillating packer; sweep panel crank arms pivot in slide blocks
The LINEA-line bodies
    The new Norba rear loaders were also different compared to previous bodies in other aspects, and with the overall update the bodies gained the LINEA designation. The bodies now lacked the traditional stiffener beams on the outside, and instead these were integrated with the wall elements. The wall elements were shorter than the traditional side wall plates, and had a semi-circular flange bent 90° outwards. The wall elements were then welded together, and the result was a lighter weight, higher strength body compared to traditional methods. Another advantage was that holes for electrical wiring, and hydraulic hoses could be cut into the elements before the bending operation. As the elements were laser cut, and then bent, any desirable shape or interface could easily be integrated during the relatively cheap manufacturing process. The holes also acted as weight reduction, thus providing multiple benefits. Simple steel plates were then welded to the outer curved flanges of the wall elements to add extra strength.
    The sides of the bodies were then fitted with plastic sheets that gave an impressive, smooth appearance. Company logotypes and other patterns could easily be printed on these sheets, and the Norba logotype and model name was almost always found in the upper front corners. The sheets were held in place by lightweight aluminum profiles, which were fixed with standard screws to the inner body superstructure. The lower end of the sides were also covered with a large anodized aluminum profile, and on later versions the tailgate operating buttons were attached to it. The roof and bottom sides however, were not covered with plastic sheets, but were instead kept "open" for easier access. This concept might be seen as a transition towards a curved body construction, where the "strength of the arc" was used in the stiffeners, but the inner body retained a rectangular cross-section.
Front view of the "Linea" body construction, a composite welded inner wall with curved plastic outer skins.
Also note the downward slope of the tailgate roof, unique to the RL30 model
Rear view shows the elliptical shape of the hopper bottom, and access panels for slide ram, and the tailgate lift ram
The RL25 was dimensionally smaller, and is easily identified by its 'flat' tailgate roofline
SELECTED PATENTS
Patent # |
Description |
Inventor |
Assignee |
Date |
US4955776A |
Apparatus for charging solids under compression... |
Dahlin |
Norba |
February 15, 1988 |
10/13/19
© 2019
All Rights Reserved
Logos shown are the trademarks of respective manufacturers
Photos from factory brochures/trade advertisements except as noted
|
|
| |