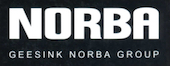
Norba RL 200 / RL 300 / RL 50 / MF 300 / N4
    In 2000, Norba was acquired by Netherlands-based Geesink, becoming a division of Geesink Norba Group, though production remained within Sweden for a few more years. The following year, Geesink-Norba was itself bought by USA-based Oshkosh Corporation which owned the McNeilus brand of refuse packers. With the arrival of the new millennia, Norba made a major revision of their product line. With this revision they entered the curved shell era of refuse bodies, with the new models now identified as 100-series rear loaders. Although the previous LINEA bodies in the 10-series had been "semi-curved", this time it was the real thing. The new bodies were curved all over, both sides, roof and floor. The curved metal sheets were held by a sturdy framework, surrounding all corners of the body. The lower side bolster housed controls for tailgate lift, and various other functions. The ejector plate was redesigned as well, and the guide tracks were replaced with a single H-beam at the center of the floor.
Norba 100-series ejector design
    The old tailgate lock mechanism, which required an initial upward sliding motion of the tailgate, was replaced. The new locking system was based on one patented by McNeilus in 1992, but never used on their own bodies. The vertically placed tailgate lift cylinders (5) were no longer connected directly to the rear side faces of the body, but instead connected to levers (9). The cylinders were connected to the rear end of the levers, and at the front ends the locking rods (8) were connected. The fixed hinge point (9) was positioned near the middle of these levers, and both the front of the levers and the locking rods were concealed inside the main rear stiffener beams. As the cylinders pushed the rear part of the levers downward, the front half pulled the rods upwards, and cleared the adjustable latches (15) which were attached to the tailgate. The rear part of the levers travelled a limited arc, before hitting a solid stopper plate (12), which forced the cylinders to start opening the tailgate.
Locking mechanism unlatched, just before the cylinders start lifting the tailgate
    As Norba and McNeilus had a common ownership at the time through Oshkosh, this technology seems to have been transferred to Norba, who patented the solution on the European market in 2001. The new system was safer, and also reduced the wear on the rubber seal between body and tailgate, as the abrasive sliding motion was removed.
NORBA RL 300
Norba RL 300 with container winch and bin lifter
    The biggest of the new rear loader family members was the RL 300. It was the direct successor to the RL-35, and the packer assembly was identical. Like the RL-35 it had a swept volume of 1.7m3 (2.22yd3) and the slide cylinder stroke was 800mm. Compaction pressure was rated at 2.4kg/cm3, which is equivalent to nearly 30 tons of force. The tailgate was almost identical as well, but the tailgate roof was now sloping rearwards, unlike the RL-35 which was horizontal. The upper rear side stiffener beams were also removed and the lower hopper side walls were rounded off to follow the circular contour of the hopper floor. The RL 300 was intended for heavier duty, and at this job it excelled. It was offered with a wide range of bin/container lifting options, and a "dust free" bin lifter system was offered as well. The latter required a slightly redesigned tailgate, with an extended rear vertical profile. If the dust free option was chosen, the vehicle could however only be used to empty bins up to 1m3. Body sizes ranged from 13.5 to 26.6m3.
NORBA RL 200
    The RL 200 was actually fairly hard to distinguish from its larger sibling, unless the specific differences are known. The RL 200 packer plate had a shorter distance from the edge to the hinge, giving it a smaller surface area. The swept volume was smaller, rated at 1.6m3 (2,09yd3) with 800mm slide travel. Smaller diameter cylinders were used to operate both slide and packer panel. Compaction pressure was rated at 2.2kg/cm3, and the smaller packer surface area resulted in a smaller total force, somewhere above 20 tons. The changed packer blade size also affected the outer silhouette of the tailgate, and since the slide tracks were positioned the same way as on RL 300, the difference was compensated by the angle between the tailgate and body. The RL 300 had an angle of 80°, but the RL 200 had a less steep angle. As a consequence, the RL 200 bodies were not entirely identical to those of the RL 300. Another giveaway was that the rear vertical part of the tailgate was angled forward at a lower point, increasing the slimmer appearance of the tailgate.
    The RL 200 was intended for lighter duty, but was offered with exactly the same bin/container options as the RL 300, including the "dust free" system. Like the RL300 it was normally a full-width rear loader, but a narrow version was offered as well. Both the full-width and the narrow versions were also available with reduced total height, to be able to handle routes with strict height limits. The low height version had a horizontal tailgate roof, but the rest of the tailgate and packer assembly was basically identical to the full height version.
RL 200 about to unload at the incineration plant
Comparison of body and tailgate shapes between the RL 300 and RL 200
Another low height RL 200, with a foldable hopper extension. This type of extension can be used on tailgates with container slots as well,
making the vehicle extremely flexible. Note the significantly smaller packer blade compared to the RL 300.
NORBA RL 50
    To replace the Ki-15 on the really small routes, Norba offered a third single stream rear loader: the RL 50. It was significantly smaller than the two others, and was intended for really small alleys and parks. The overall body construction was very similar to the RL 200/RL 300, except for the inability to empty large containers. It was also equipped with a bin lifter as standard, and the maximum bin size was 660L. The overall body capacity was
4.4 to 5.4m3 and the swept hopper volume was 0,85m3. The packer compaction pressure was rated at 1.75kg/cm2. The RL50 was discontinued fairly soon after its launch, and the explanation seems to have been that it was way too expensive to produce in relation to its sales price. This is not very surprising, considering that it was almost as advanced as the larger siblings. The savings on material weight alone couldn't reduce the price enough to appeal to customers.
NORBA MF 300
    To cope with the increasing demand for multi-faction bodies, Norba updated the MF35 as well, and the result was named MF 300. This is a fairly misleading name though, as the tailgate, body and packer (apart from being split into two) are much more similar to the RL 200. The entire body was split into two separate volumes, with a ratio of approximately 40/60. Unlike the MF35, the two tailgate compartments were entirely separated, and each one could be lifted separately. This approach virtually eliminated the risk of cross-contamination, and also made the unloading order irrelevant. The individual tailgates were raised by a single lift cylinder each, placed on the outer sides, just like on the single stream rear loaders. In the beginning, the MF300 was only available with the E-option for the tailgate, which means that the rear walls extended vertically all the way up to the roof. Later versions however are also available with the typically angled rear silhouette. The reason for this is that there are multiple lifter systems to choose from.
MF 300 had individual tailgates rather than the divided hopper of the MF35
NORBA N4
    In the early summer of 2007, fifty positions were transferred from the Norba factory at Blomstermala to the Kalmar facility. By September, the Blomstermala factory was abruptly closed, ending 70 years of Norba refuse truck production. Most of the jobs were moved to Geesink plants in The Netherlands. In 2009, Oshkosh Corporation sold Geesink-Norba to private investors, and the company is currently operating under independent ownership. Virtually all refuse production is now in The Netherlands, with a good deal of technical sharing with the Geesink product line.
    The latest rear loader from Norba (Now Geesink Norba Group) is the N4. It is a totally reworked version of the RL 300, and virtually nothing is interchangeable between the two different versions. The body has been changed into the one from the newly developed Geesink GPM4 rear loader, and the tailgate shape has been adapted significantly in order to make this possible. The 80° angle between the tailgate and body has been replaced with the fully vertical interface in the GPM4, a very unusual feature on a slide/sweep rear loader. Tailgate lift cylinders are no longer vertical, but instead slope backwards. The packer assembly has been completely updated as well, but its Norba heritage is still recognizable. It is unknown if the tailgate has been engineered in Sweden, or by Geesink Norba in the Netherlands.
10/13/19
© 2019
All Rights Reserved
Logos shown are the trademarks of respective manufacturers
Photos from factory brochures/trade advertisements except as noted
|
| |