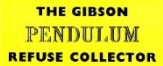
John Gibson & Son Ltd.
Edinburgh, Scotland
    Beginning with a sales and repair facility for Morris Commercials, Gibson also designed their own refuse collection body called the Pendulum. Their literature claimed they had produced "pendulum" bodies since the 1930s, but the first patents were granted in 1950. The Pendulum was a "swinging gate" type packer, similar to models made by Sovel and Glover, Webb & Liversidge, but with some novel features. The Pendulum's swinging packer plate was operated by a single hydraulic ram located on the body floor, rather than in the roof. The ram was connected to the packer plate with a pin, which was removed prior to tipping the body during unloading.
    The packer plate was also unique in that it was not flat, but was shaped with two pressure surfaces of varying angles. This helped to better compact refuse within the body as it filled. Pendulums were used on hand-loaded routes, and later models were fitted with Paladin binlifts for bulk collection. Discharge was by tipping, with roof-mounted linkage which automatically opened the end gate as the body was raised.
Hand-loading Pendulum through opened hopper doors
Pendulum compression cycle
Hopper detail showing dual pressure faces of packer plate, and locking loading doors
SECOND GENERATION PENDULUM
    The tailgate lift linkage was modified for 1957, but a more significant change occurred in 1961 when the packer plate ram was relocated from the floor of the body to the chassis frame. The end of the ram was connected to the packer plate was now by a roller-hook arrangement. The ram automatically disengaged from the packer whenever the body was raised, alleviating the need for the manually removed pin. Several feet of hydraulic piping were eliminated with this change. The 1960s saw a variety of binlifts offered for the Pendulum range.
For 1961, the packer cylinder (20) was relocated to the vehicle chassis frame
1962 Pendulum on a short-wheelbase Dennis Heron chassis
    Introduced in 1953, the Paddle Packer complimented the Pendulum models. Though not commercially successful, it did foreshadow the coming trend towards revolving-blade packers in the UK. The Paddle Packer actually had two opposed packer blades, hinged to a revolving crank arm and powered by hydraulic cylinders mounted on the hopper sidewalls. This requires switch gear for the hydraulic valve, since the rams must change direction every half-revolution of the mechanism. It was ambitious engineering for the early 1950s, and variations of this arrangement were later used on the popular SEMAT Superpac and SD Revopak over a decade later.
Diagram of the rotary crank and twin packer blades
Side view showing hydraulic cylinder and crank arm. Hopper cover is spring-balanced
For simplicity, the tailgate was raised by a single fixed cable as the body was tipped
THE FINAL YEARS
    Gibson unveiled a continuous loader with the 1967 C-Series This design had a pendulum-like swinging packer blade with a curved follower plate, which moved beneath the loading rave. Once pushed into the body, the each hopper load was crushed by a downward-sliding block, which also served to retain the refuse within the body. Initially, discharge was by tipping.
    Another interesting innovation from Gibson was the use lightweight, reinforced aluminum sheeting for body panels. This was made in Gibson's own shop, and began appearing on truck bodies in 1969. Both the Pendulum and C-Series received the new panels, the latter also being fitted with an ejection-discharge plate by 1970. Despite noble engineering efforts, the small firm succumbed to mounting financial difficulties and was liquidated in mid-1971. Caleden Engineering was slated to take over sales and service of the Gibson line, including a recently announced Multiversal, but this arrangement does not appear to have lasted very long, and it is unclear if the Multiversal was actually built. By 1972, the Pendulum returned briefly in the product line of Eagle of Warwick.
C-series used swinging pusher plate (red) and vertical crusher-reatiner plate
Crusher-retainer plate retracts as pusher plate swings inward
C-series ejection-discharge version with ribbed aluminum bodywork
9/7/15
© 2015
All Rights Reserved
Logos shown are the trademarks of respective manufacturers
Photos from factory brochures/trade advertisements except as noted
|
| |